Process meter calibration is a elementary facet of guaranteeing the accuracy and reliability of devices utilized in industrial processes.
Process meter calibration is a elementary side of guaranteeing the accuracy and reliability of devices utilized in industrial processes.
Objective of Calibration:
The primary purpose of calibration is to confirm and adjust the accuracy of course of meters to ensure that they supply exact and reliable measurements.
calibrate process meter of Process Meters:
Process meters encompass a selection of devices, together with stress gauges, temperature sensors, flow meters, level transmitters, pH meters, and more. Calibration procedures are particular to the sort of meter and the parameter being measured.
Calibration Standards:
Calibration includes comparing the readings of the method meter with a reference normal of recognized accuracy. These requirements must be traceable to national or international measurement requirements.
Traceability:
Traceability ensures that the calibration process could be traced again to a recognized standard, providing confidence in the accuracy of the measurements.
Calibration Procedure:
The calibration course of sometimes includes adjusting the method meter to match the readings of the reference normal. Calibration procedures are specific to every type of instrument.
Calibration Equipment:
Specialized calibration tools is used, corresponding to pressure calibrators, temperature baths, circulate calibrators, and electrical calibrators, depending on the sort of process meter.
Calibration Interval:
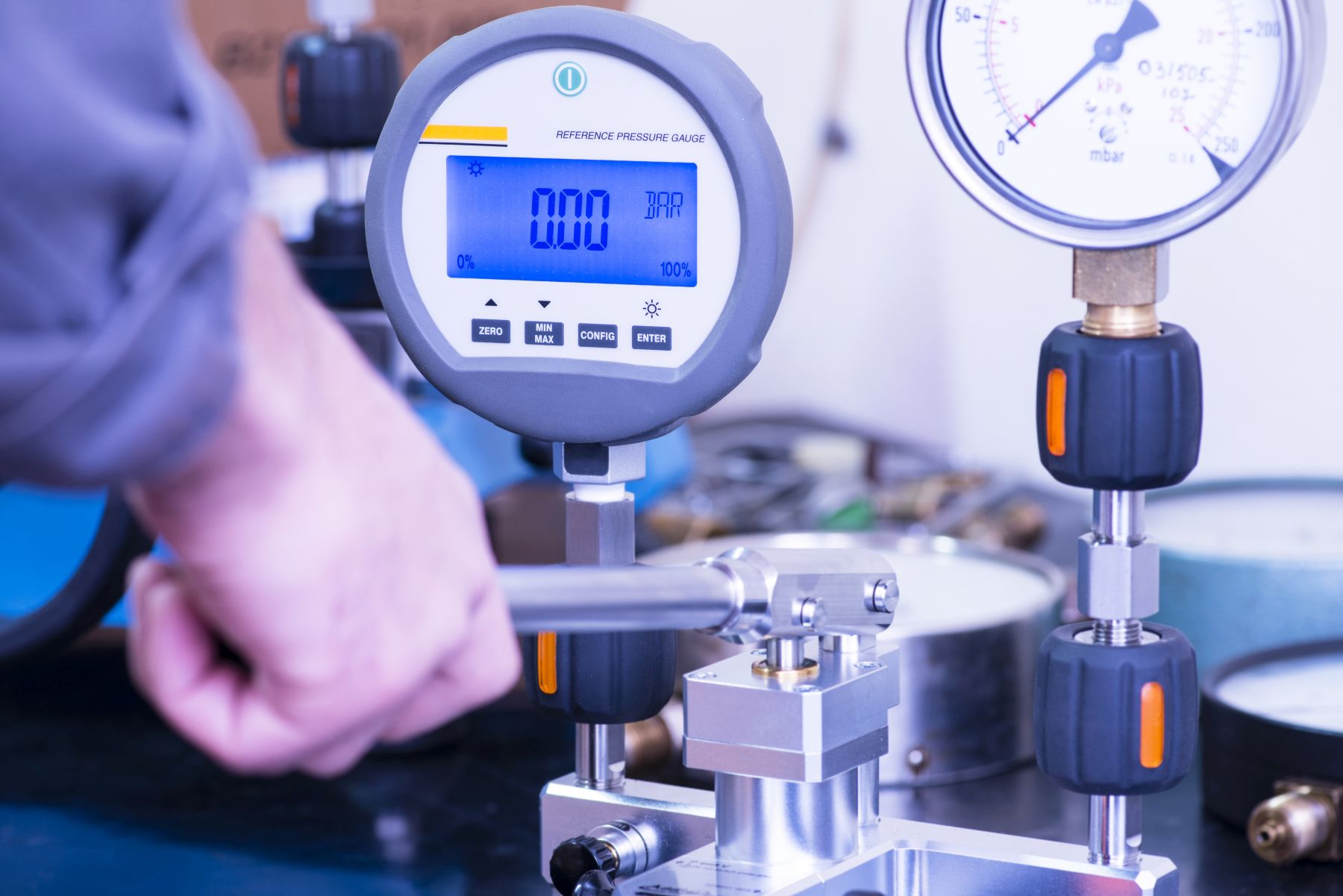
Calibration intervals are decided based on components similar to business requirements, producer suggestions, and the criticality of the measurements. Regular calibration at defined intervals ensures ongoing accuracy.
Documentation:
Detailed documentation is a crucial part of the calibration process. Calibration records embrace data such because the date of calibration, tools used, calibration standards, adjustments made, and the technician's signature.
Calibration Certificates:
Calibration labs provide certificates after the calibration course of, indicating the as-found and as-left conditions of the instrument. These certificates function evidence of compliance with accuracy requirements.
Adjustment and Repair:
If the process meter is found to be out of calibration, adjustments or repairs may be essential to deliver it back inside the specified accuracy limits.
Calibration Tolerances:
Each instrument has outlined tolerances that specify the appropriate vary of deviation from the true worth. Calibrations ensure that the instruments fall within these tolerances.
On- https://bodaciousshopsjanesville.com/members/sortlung0/activity/378274/ :
Some calibration actions can be carried out on-site, reducing the want to take away devices from the process. On-site calibration is especially helpful for important processes the place downtime must be minimized.
Calibration Management System:
Organizations might use a calibration management system to schedule, monitor, and manage calibration activities systematically.
By following these basics, organizations can keep the accuracy and reliability of their process meters, making certain that they persistently meet high quality requirements and regulatory necessities. Regular calibration is important for the correct functioning of industrial processes and the production of reliable information..