Process meter calibration is a basic facet of ensuring the accuracy and reliability of devices utilized in industrial processes.
Process meter calibration is a basic facet of making certain the accuracy and reliability of devices utilized in industrial processes.
Objective of Calibration:
The major function of calibration is to confirm and modify the accuracy of process meters to ensure that they provide exact and reliable measurements.
Types of Process Meters:
Process meters embody a selection of instruments, together with stress gauges, temperature sensors, flow meters, stage transmitters, pH meters, and extra. Calibration procedures are specific to the type of meter and the parameter being measured.
Calibration Standards:
Calibration includes evaluating the readings of the process meter with a reference commonplace of recognized accuracy. These standards should be traceable to national or international measurement requirements.
Traceability:
Traceability ensures that the calibration process could be traced back to a acknowledged commonplace, providing confidence within the accuracy of the measurements.
Calibration Procedure:
The calibration course of sometimes entails adjusting the process meter to match the readings of the reference normal. Calibration procedures are specific to each kind of instrument.
Calibration Equipment:
Specialized calibration equipment is used, such as stress calibrators, temperature baths, circulate calibrators, and electrical calibrators, depending on the type of process meter.
process meter calibration basics :
Calibration intervals are determined based mostly on elements such as business requirements, producer recommendations, and the criticality of the measurements. Regular calibration at outlined intervals ensures ongoing accuracy.
Documentation:
Detailed documentation is a crucial part of the calibration process. Calibration records embody data such because the date of calibration, gear used, calibration requirements, adjustments made, and the technician's signature.
Calibration Certificates:
Calibration labs present certificates after the calibration process, indicating the as-found and as-left conditions of the instrument. These certificates function proof of compliance with accuracy requirements.
read more and Repair:
If the process meter is found to be out of calibration, adjustments or repairs could additionally be necessary to deliver it back throughout the specified accuracy limits.
Calibration Tolerances:
Each instrument has outlined tolerances that specify the acceptable vary of deviation from the true value. Calibrations make positive that the devices fall inside these tolerances.
On-Site Calibration:
Some calibration activities can be performed on-site, decreasing the need to take away instruments from the process. On-site calibration is particularly useful for important processes the place downtime should be minimized.
Calibration Management System:
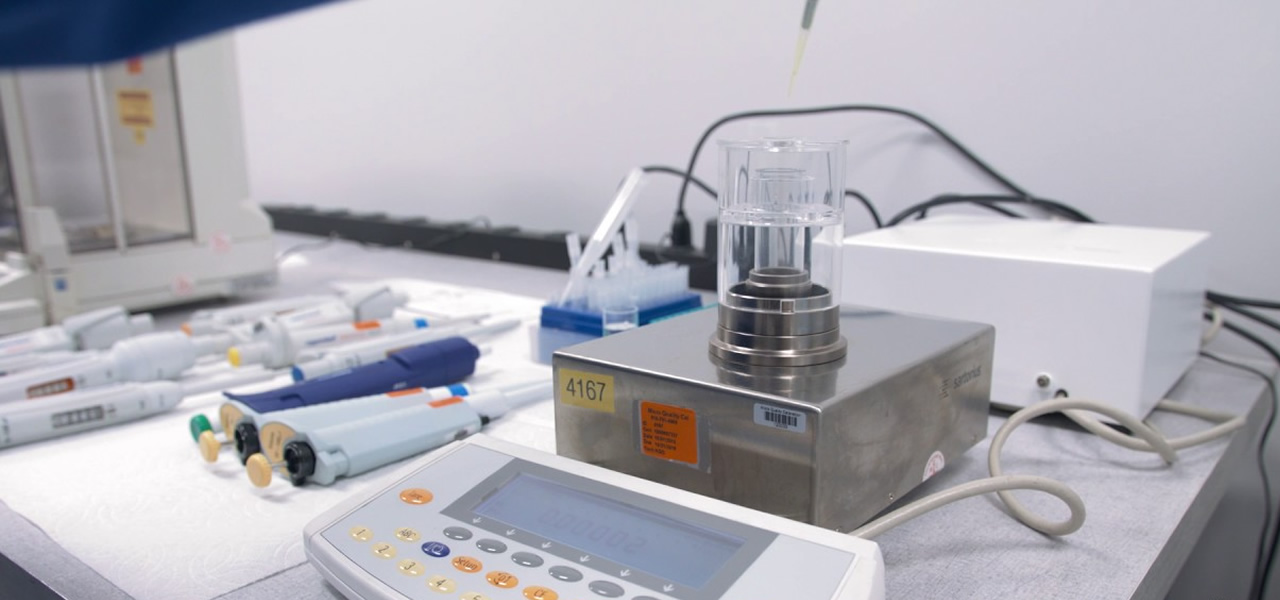
Organizations could use a calibration management system to schedule, track, and handle calibration activities systematically.
By following these fundamentals, organizations can preserve the accuracy and reliability of their process meters, ensuring that they persistently meet quality standards and regulatory necessities. Regular calibration is important for the correct functioning of business processes and the production of reliable knowledge..